guide chain
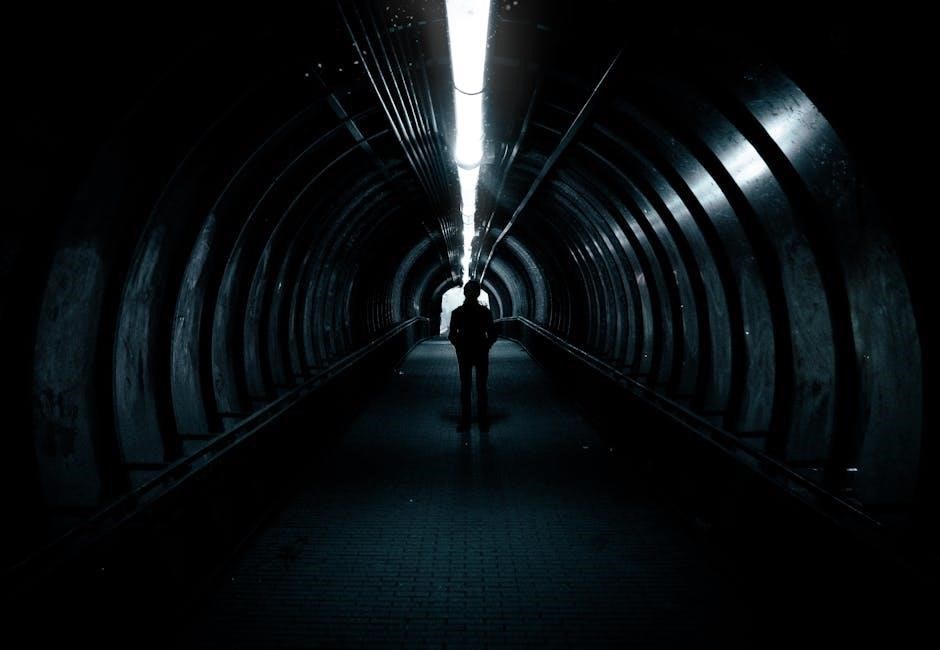
Guide chains are essential components in conveyor systems‚ ensuring smooth material flow and preventing damage. They are durable‚ designed for heavy-duty applications‚ and require minimal maintenance for optimal performance.
1.1 Definition and Purpose
A guide chain is a mechanical component used to guide and support moving parts in conveyor systems‚ ensuring smooth operation and alignment. Its primary purpose is to maintain proper positioning of materials or products as they move along the production line‚ reducing wear and tear on equipment. Designed for durability‚ guide chains play a critical role in industrial automation‚ enhancing efficiency and reliability in various manufacturing processes.
1.2 Historical Development
The concept of guide chains traces back to the Industrial Revolution‚ where early chains were crafted from iron and steel. Initially simple in design‚ these chains were used to convey goods in rudimentary conveyor systems. Over time‚ advancements in metallurgy and engineering led to more durable and versatile guide chains. The introduction of standardized manufacturing processes in the 20th century further refined their design‚ enabling widespread use in industrial applications. Today‚ guide chains remain a cornerstone of modern material handling systems.
Components of a Guide Chain
Guide chains consist of links‚ pins‚ and attachments‚ designed to provide durability and flexibility. These components ensure smooth operation in various industrial applications.
2.1 Links and Pins
Links and pins are the fundamental components of guide chains‚ providing structural integrity and flexibility. Links form the chain’s framework‚ while pins act as connectors‚ ensuring smooth articulation. Constructed from durable materials like steel or alloy‚ they are designed to withstand heavy loads and repetitive motion. Proper alignment and secure fitting of pins within links are crucial for reliable operation. High-quality manufacturing ensures minimal wear‚ reducing the risk of chain failure in demanding environments. Regular inspection and maintenance of these components are essential for optimal performance.
2.2 Attachments and Special Features
Attachments and special features on guide chains enhance their functionality and adaptability. These include hooks‚ brackets‚ and customized connectors to suit specific applications. Special features like coatings or reinforced materials improve durability in harsh environments. Some chains incorporate anti-wear technologies or silent operation designs for reduced noise. Attachments can also enable quick installation or easy integration with other system components. These enhancements ensure guide chains meet diverse operational demands‚ making them versatile for various industrial and material handling needs.
Types of Guide Chains
Guide chains are categorized into standard‚ heavy-duty‚ and customizable types. Each offers distinct features tailored to specific industrial needs‚ ensuring optimal performance across various applications and environments.
3.1 Standard Chains
Standard guide chains are the most commonly used type‚ designed for general-purpose applications in conveyor systems. They are made from durable materials like steel or plastic‚ ensuring longevity. These chains are ideal for light to medium-duty operations‚ offering reliable performance in various industrial settings. Their straightforward design makes them easy to install and maintain‚ with regular lubrication and inspection recommended to prolong their service life. Standard chains are versatile and cost-effective‚ making them a popular choice for many industries.
3.2 Heavy-Duty Chains
Heavy-duty guide chains are engineered for demanding applications‚ offering exceptional strength and durability. Constructed from robust materials like reinforced steel‚ these chains are designed to withstand high loads‚ extreme temperatures‚ and harsh environments. They feature thick‚ wear-resistant links and advanced coatings to minimize corrosion; Ideal for industries requiring heavy lifting and rigorous performance‚ heavy-duty chains ensure reliable operation in challenging conditions. Regular maintenance‚ such as lubrication and inspection‚ is essential to maintain their longevity and functionality in industrial settings.
3.3 Customizable Chains
Customizable guide chains offer tailored solutions to meet specific application requirements. They can be modified in length‚ material‚ and attachment points to suit unique operational needs. Industries like automotive manufacturing and specialized machinery benefit from these adaptable chains. With options for corrosion-resistant coatings and reinforced links‚ customizable chains enhance durability and performance. They are ideal for applications requiring precise alignment and flexibility‚ ensuring optimal efficiency in diverse industrial environments while minimizing wear and tear on connected components.
Applications of Guide Chains
Guide chains are widely used in industrial conveyor systems‚ automotive manufacturing‚ and material handling equipment‚ ensuring smooth operation and efficient material transportation across various industries.
4.1 Industrial Conveyor Systems
Guide chains play a crucial role in industrial conveyor systems by aligning and guiding conveyor belts to ensure smooth material flow. They are designed to handle heavy loads and reduce wear on the system. In manufacturing and logistics‚ guide chains enhance efficiency by maintaining belt alignment‚ preventing misalignment issues that could lead to downtime. Their durability and low maintenance requirements make them indispensable in high-volume production environments‚ ensuring continuous operation and minimizing disruptions in industrial settings.
4.2 Automotive Manufacturing
Guide chains are integral to automotive manufacturing‚ where they ensure precise alignment and movement of components during assembly. Their durability and resistance to wear make them ideal for high-speed production lines. In robotic systems and tooling‚ guide chains facilitate smooth transitions between assembly stages‚ enhancing operational efficiency. By maintaining consistent alignment‚ they reduce downtime and improve overall production quality‚ making them a critical component in modern automotive manufacturing processes and automation systems.
4.3 Material Handling Equipment
Guide chains play a vital role in material handling equipment‚ ensuring smooth and efficient movement of goods. They are commonly used in conveyors‚ lift trucks‚ and sorting systems to guide loads securely. Their durability and resistance to wear make them ideal for heavy-duty operations. By maintaining precise alignment and minimizing friction‚ guide chains enhance operational efficiency and reduce downtime. This ensures consistent and reliable material flow‚ making them indispensable in modern logistics and warehousing systems.
Choosing the Right Guide Chain
Choosing the right guide chain involves considering load capacity‚ environmental conditions‚ and alignment needs. Selecting the appropriate type ensures optimal performance and longevity in various applications.
5.1 Load Capacity Considerations
Load capacity is crucial when selecting a guide chain. It must handle the maximum weight it will carry without compromising performance or longevity. Factors like material strength‚ chain dimensions‚ and system requirements influence this decision. Choosing a chain with adequate load capacity ensures smooth operation and prevents premature wear. Always align the chain type with the specific demands of your application to avoid overload risks. Refer to manufacturer guidelines for precise specifications and recommendations.
5.2 Environmental Factors
Environmental factors significantly influence the selection and performance of guide chains. Chains exposed to corrosive or high-temperature environments require specialized materials to withstand these conditions. For example‚ stainless steel chains are ideal for corrosive settings‚ while heat-resistant chains are suited for high-temperature applications. Proper lubrication is essential in dusty or dirty environments to prevent wear. Ensuring the chain’s material aligns with its operational environment ensures optimal performance and extends its lifespan‚ making it crucial for reliable operation.
5.3 Alignment and Accuracy
Proper alignment and accuracy are critical for guide chains to ensure smooth operation and prevent wear. Misalignment can lead to increased wear on chains and components‚ reduced efficiency‚ and noise. Regular inspections and precise installation are essential to maintain accurate alignment. Proper tensioning and adjustment of chain components help mitigate misalignment issues. Accurate alignment ensures optimal performance‚ minimizes downtime‚ and extends the service life of the chain and associated equipment.
Maintenance and Repair
Regular maintenance ensures guide chains operate efficiently. Inspections‚ lubrication‚ and timely replacement of worn parts prevent breakdowns and extend service life effectively.
6.1 Regular Inspection
Regular inspection of guide chains is crucial for maintaining optimal performance and preventing unexpected failures. Visual checks for wear‚ misalignment‚ and damage should be conducted frequently. Inspect pins‚ links‚ and attachments for signs of fatigue or corrosion. Proper alignment ensures smooth operation and prevents uneven wear. Monitoring chain tension and lubrication levels is equally important. Regular inspections help identify potential issues early‚ reducing downtime and extending the chain’s service life.
6.2 Lubrication and Cleaning
Lubrication and cleaning are vital for maintaining guide chain efficiency and longevity. Apply high-quality‚ waterproof lubricants to moving parts to reduce friction and prevent corrosion. Regularly clean the chain to remove dirt‚ grease‚ and debris that can cause wear. Avoid using harsh chemicals or abrasive materials that may damage the chain’s surface. Proper lubrication and cleaning ensure smooth operation‚ reduce maintenance costs‚ and extend the chain’s lifespan. Regular attention to these tasks is essential for optimal performance.
6.3 Replacement of Worn Parts
Replacing worn parts is crucial for maintaining guide chain performance and safety. Regularly inspect for wear and tear‚ especially on pins and links. Replace damaged components promptly with genuine parts from the manufacturer to ensure compatibility and durability. Proper tools and safety measures must be used during replacement to avoid accidents. Timely part replacement prevents system breakdowns and extends the chain’s lifespan‚ ensuring smooth and reliable operation in industrial environments.
Safety Precautions
Ensure proper installation‚ follow operational guidelines‚ and implement emergency protocols to prevent accidents. Regular training and adherence to safety standards are essential for safe guide chain operations.
7.1 Proper Installation
Proper installation of guide chains is critical to ensure safe and efficient operation. Align the chain correctly‚ tension it as specified‚ and secure all components firmly. Use appropriate tools and follow manufacturer guidelines to prevent misalignment or loose connections. Regularly inspect the setup to ensure stability and functionality. Improper installation can lead to accidents‚ equipment damage‚ or system downtime. Always adhere to safety protocols and consult professionals if unsure. Proper installation ensures optimal performance and minimizes risks.
7.2 Operational Safety Measures
Ensure all personnel wear protective gear‚ including gloves and safety glasses‚ when working near guide chains. Regularly monitor chain tension‚ alignment‚ and wear during operation; Install emergency stop systems and ensure they are easily accessible. Train employees on proper handling and emergency procedures. Keep loose clothing and long hair tied back to avoid entanglement. Maintain clear walkways around conveyor systems to prevent tripping hazards. Adhere to manufacturer guidelines for safe operational practices and conduct frequent inspections to identify potential risks early.
7.3 Emergency Procedures
In case of a guide chain malfunction‚ immediately stop the system and isolate power sources. Evacuate the area and contact trained personnel. Inspect the chain and surrounding equipment for damage. Document the incident and implement corrective actions to prevent recurrence. Replace any damaged components before resuming operations. Ensure all safety protocols are followed to restore safe working conditions. Regular emergency drills can help prepare staff for such situations‚ minimizing risks and ensuring a prompt response.
The Future of Guide Chains
Advancements in materials and automation are reshaping guide chains‚ offering enhanced durability and integration with smart systems. Future designs will focus on sustainability and intelligent functionality.
8.1 Technological Advancements
Technological advancements are driving innovation in guide chain design‚ with smarter manufacturing techniques enabling stronger‚ lighter‚ and more durable chains. Automation integration allows real-time monitoring and predictive maintenance‚ optimizing performance. Advances in materials science are leading to corrosion-resistant and self-lubricating solutions‚ reducing downtime. Additionally‚ the integration of IoT and data analytics enables proactive maintenance‚ ensuring guide chains operate efficiently in demanding environments. These innovations are setting the stage for a new era of reliability and precision in industrial applications.
8.2 Material Innovations
Material innovations are transforming guide chains‚ with advancements in steel alloys‚ polymers‚ and composites enhancing durability and performance. High-strength‚ low-friction materials reduce wear and tear‚ while corrosion-resistant coatings extend service life. Lightweight yet robust options are being developed for precision applications. These innovations address industry demands for reliability‚ efficiency‚ and sustainability‚ ensuring guide chains meet the evolving needs of modern machinery and automation systems.
8.3 Integration with Automation
Guide chains are increasingly integrated with automation technologies‚ enhancing operational efficiency. Smart sensors and IoT capabilities enable real-time monitoring and predictive maintenance. Automated systems optimize chain performance‚ reduce downtime‚ and improve precision. Integration with AI-driven systems allows for adaptive adjustments‚ ensuring seamless operation in dynamic environments. This fusion of guide chains with automation technologies is revolutionizing industries‚ delivering smarter‚ more reliable‚ and high-performance solutions for modern manufacturing and material handling needs.